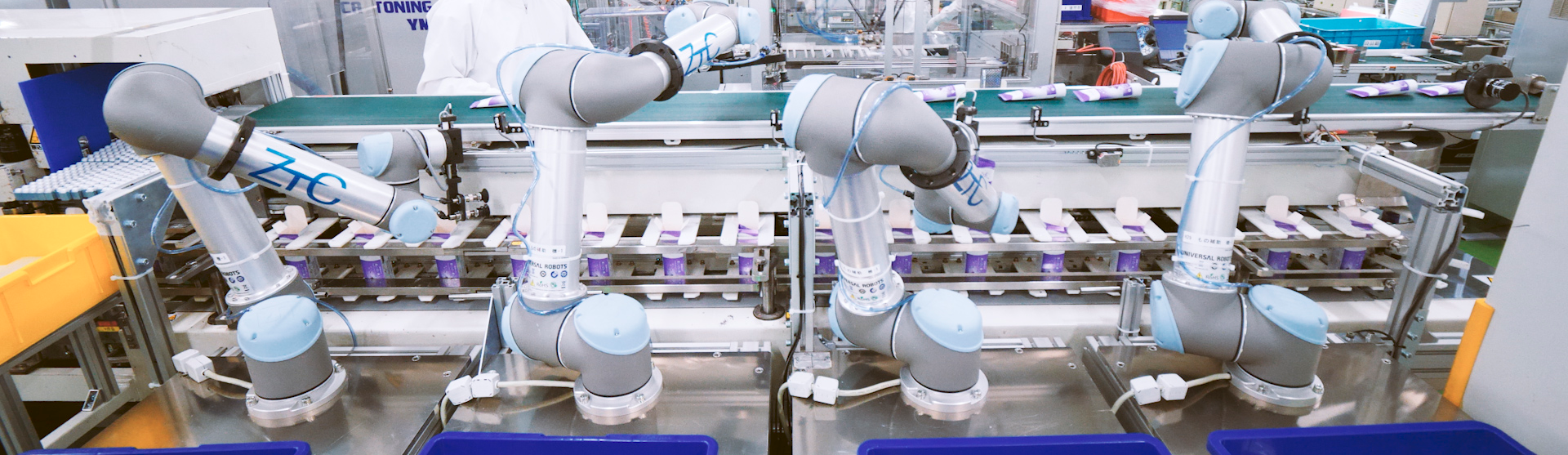
Now robots can predict their own maintenance need
Emil Stubbe Kolvig-Raun is writing an industrial PhD for Universal Robots at the Faculty of Engineering at SDU. As part of his research, he has developed an algorithm that can predict when a robot will require maintenance and repair. This could save companies from costly unexpected breakdowns in production.
In the 2011 film 'Limitless', there's a scene where the main character Eddie – played by Bradley Cooper – jumps off a balcony and grabs onto the platform below. It’s a pretty risky maneuver, but he knows he can do it because he has just made an exact calculation of the effort required.
Emil Stubbe Kolvig-Raun’s algorithm works somewhat similarly. At least, that’s how the 28-year-old software engineer likes to think about it.
Emil Stubbe Kolvig-Raun is currently finalizing his industrial PhD at the Maersk Mc-Kinney Moller Institute at the University of Southern Denmark, in collaboration with the robotics company Universal Robots and with Mikkel Baun Kjærgaard from SDU and Ralph Brorsen from UR as his supervisors.
Over the last three years, he has developed, among other things, a model that quantifies how stressed a robot is during a given piece of work, and as a result, can predict when the robot needs maintenance. This is known as predictive maintenance. The study was recently published in the journal IEEE Robotics and Automation Letters.
Just like Bradley Cooper in 'Limitless', the robot can use Emil Stubbe Kolvig-Raun’s method to calculate how much 'energy' or 'strength' it has left and how many thousands, hundred thousands, or millions of routines it can perform before needing service.
- This way, you can avoid unexpected downtime, that is, periods when the robots aren't running and you have to halt production, explains Emil Stubbe Kolvig-Raun.
- This can be quite costly for a business. And considering that a large part of global production is automated, there’s a real need for this.
Reality and expectations
Emil Stubbe Kolvig-Raun’s algorithm is designed for Universal Robots’ robotic arms but could, in principle, also be used on other robots and machines.
It just requires that they have a built-in system, for example, a safety system, that constantly monitors the robot and compares observations of reality with calculated expectations of what the robot should be like.
All cobots, or collaborative robots, like those from Universal Robots, have such a system.
- The robots are equipped with a lot of sensors that measure what's going on while the robots work. It could be what the temperature is in this joint? What is the power consumption? What is the speed?, says Emil Stubbe Kolvig-Raun.
- At the same time, there is a safety system that stands in the background and makes a lot of calculations on what we expect regarding all these parameters. And if there is suddenly a discrepancy between the two things - the expectations and reality - then the robot is programmed to stop.
That's why, unlike more traditional industrial robots, you can safely move around cobots and, as the name suggests, work together with them.
Calculate consequences
However, all the data collected by the robots can also be used to predict wear, faults, and disturbances. They would show up early as minor discrepancies between reality and expectations in the safety system, explains the PhD student.
And that’s what Emil Stubbe Kolvig-Raun has done. Specifically, the robots will be able to indicate well in advance that there is a maintenance or repair need on the way, after which the company will be able to plan a service inspection at a time that is not critical for production.
The data could also be used for other things and further develop the model, says Emil Stubbe Kolvig-Raun.
- The next step after predictive maintenance is self-maintenance. That's where the robot maintains itself, for example, by saying: Okay, the robot can see that there will be a need for maintenance after moving in a certain way 10,000 more times. But if it now performs the task a little differently and changes its movement patterns slightly, the need for maintenance can be postponed, he says.
- Essentially, we are trying to give robots the ability to practically calculate consequences and thereby compensate or self-optimize.
Meet the researcher
Emil Stubbe Kolvig-Raun is a PhD student at the Mærsk Mc-Kinney Møller Institute. He is a trained software engineer and is working on an industrial PhD in collaboration with Universal Robots. His supervisors are Mikkel Baun Kjærgaard and Ralph Brorsen from, respectively, SDU and Universal Robots. The PhD project has been funded by DIREC.